PROJECT OLIN
This project was an assessment of the feasibility of implementing energy-saving window technologies for Olin Hall, a building at Cornell University. Another goal of the project was to build a granular energy model of Olin Hall that could be used in future analysis.
Our work can be broken down into three phases: building the model exterior, modeling the building interior and HVAC (Heating, Ventilation, and Air Conditioning) system, and running simulations of the Olin Hall model with different window technologies in place.
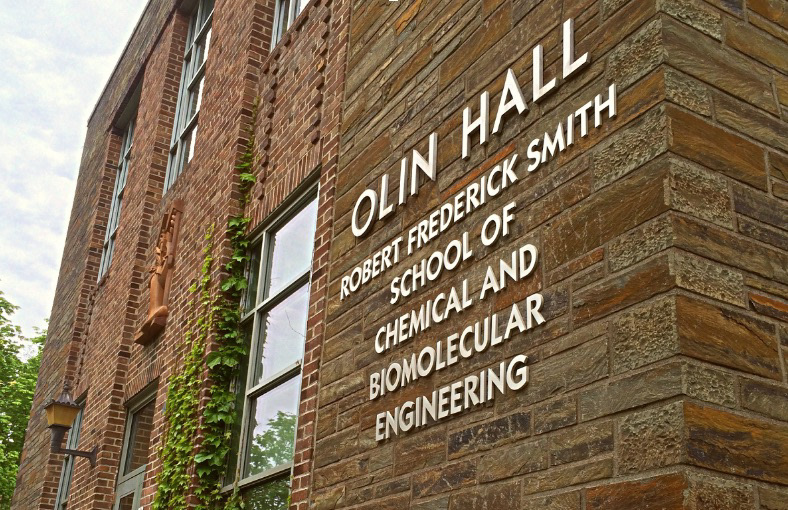
To accurately represent Olin Hall in the digital model, we recorded measurements of Olin Hall--the external perimeter, the locations and dimensions of windows and doors, the dimensions of hallways, and the locations and sizes of rooms. Because complete floor plans for Olin Hall are not available, we gathered our own internal measurements and measured the perimeter of the building. We took window measurements using string that we cut to match building dimensions and then measured with a ruler. We compared our external dimensions with measurements obtained from the Google Maps and Earth ruler tool, confirming that the margin of error was about 10% or lower, a source of error deemed acceptable by our advising professor, who had experience with the industry standards.
Once we obtained these measurements, we began to input them into DesignBuilder to create a 3D model of our building. The chosen climate for the model used the Binghamton template--the geographically closest option in the DesignBuilder databases.
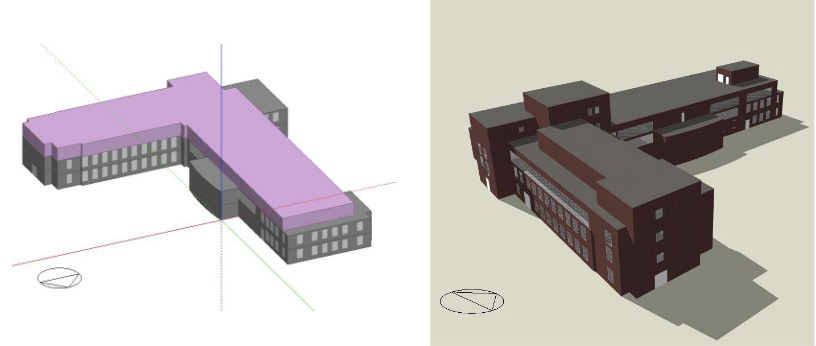
We then moved on to the second phase: modeling the interior building systems. These systems included heating, which is done through a direct hot water system; cooling, which is done through a chilled beam system; and air exchange, which is accomplished through air handling units that remove air from the building and bring in air from the outside. This phase of our process is detailed in the following sections. We also added “Scheduling”, which allowed us to model building occupancy and what types of activity were going on in the building at what times.
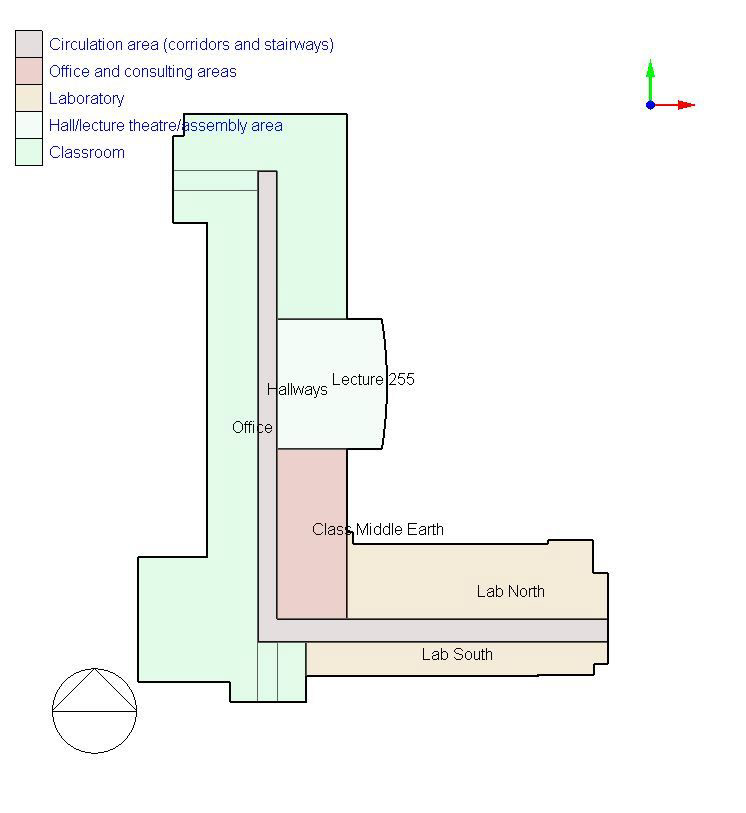
Once we had a working model of Olin Hall that accurately reflected the building as it is now, we moved into the third and final phase: running the simulations of the window technologies. The main technologies we looked at were low emissivity coatings, conventional multi-layer windows, and heat/light sensitive glass.
Our method for selecting a technology involved first determining the raw kilowatt hours of energy saved by each technology according to the DesignBuilder model of Olin Hall, as compared to the DesignBuilder model in baseline conditions. Because the only factor changed in each technology simulation was on the windows, we assumed that all energy savings were due to windows.
Once we had energy savings numbers for each technology, we found these savings as a percentage of Olin Hall’s actual current energy use for heating, electricity, and cooling, which we found from Facilities data.
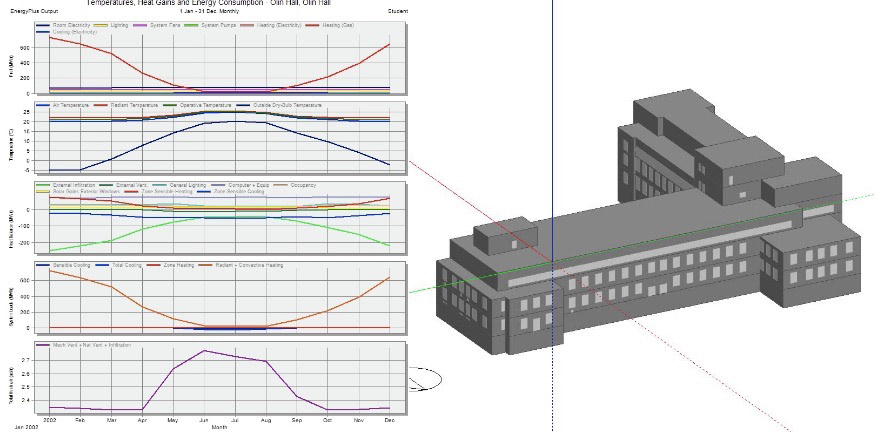
After determining the energy savings of the technologies, we conducted analysis of the second part of our calculations: cost. For a majority of the technologies, we retrieved information on costs from the supplier’s website and made an effort to get values that would be as close to what Cornell can expect to pay as possible,

Based on our analysis, we recommended Low E coatings, as they give the greatest energy savings per cost and pay back in an appropriate number of years.